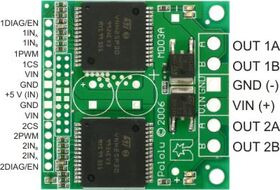
VNH3SP30 and VNH2SP30 Comparison |
||
|
VNH3SP30 |
VNH2SP30 |
Operating supply voltage (Vcc) |
5.5 – 36 V* |
5.5 – 16 V |
Maximum current rating |
30 A |
30 A |
MOSFET on-resistance (per leg) |
34 mΩ |
19 mΩ |
Maximum PWM frequency |
10 kHz |
20 kHz |
Current sense |
none |
approximately 0.13 V/A |
Over-voltage shutoff |
36 V* |
16 V minimum (19 V typical) |
Time to overheat at 20 A** |
8 seconds |
35 seconds |
Time to overheat at 15 A** |
30 seconds |
150 seconds |
Current for infinite run time** |
9:00 AM |
14 A |
*Manufacturer specification. In our experience, shoot-through currents make PWM operation impractical above 16 V.
Pololu 707/708 VNH2SP30/VNH3SP30 Dual Motor Driver Carrier MD03A 708 707
- Brand: Pololu
- Product Code: Pololu-Dual-Motor-Driver-Carrier-MD03A
- Reward Points: 178
- Availability: In Stock
- रo 17,634.00
-
रo 14,932.00
- Price in reward points: 17776
-
- 2 or more रo 17,492.00
- 4 or more रo 17,350.00
- 8 or more रo 17,207.00
Available Options
Related Products
L298N Motor Driver Board
The L298N driver module, using ST' L298N chip, can directly drive two 3-30V DC motor, and provide a ..
रo 195.00
L298P 2A Motor Shield For Arduino
This DFRobot Arduino Compatible Motor Shield (2A) uses L298P chip which allow to drive two 7-12V DC..
रo 1,183.00 रo 1,364.00
L298N - Dual Full Bridge Driver
The L298N is a high voltage, high current, dual full bridge driver designed to accept standard TTL l..
रo 150.00
L298 Dual H-Bridge Motor Driver
Double H driver module uses ST L298N dual full-bridge driver, an integrated monolithic circuit in a ..
रo 2,519.00
Stepper Motor Driver A4988
A4988 is a complete microstepping motor driver with built-in translator for easy operation. This pro..
रo 140.00
1A Motor Shield for Arduino
1A Motor Shield for Arduino This Motor shield for Arduino uses L293 chip which allow to dri..
रo 1,502.00 रo 1,730.00
Stepper Motor Driver - Easy Driver A3967
Each Easy Driver can drive up to about 750mA per phase of a bi-polar stepper motor. It defaults to 8..
रo 210.00
Pololu 2134 / 2874 DRV8834 Low-Voltage Stepper Motor Driver Carrier
This is a breakout board for TI’s DRV8834 microstepping bipolar stepper motor driver. It has a pinou..
रo 602.00 रo 628.00
Pololu 2971 DRV8880 Stepper Motor Driver Carrier
This breakout board for TI’s DRV8880 microstepping bipolar stepper motor driver features adjustable ..
रo 917.00 रo 955.00
Pololu Dual 2755/2756 MC33926 Motor Driver for Raspberry Pi
This add-on board enables a Raspberry Pi B+, A+, Pi 2, or Pi 3 to drive a pair of bru..
रo 2,802.00 रo 2,919.00
Pololu 1213 Dual MC33926 Motor Driver Carrier
This dual brushed DC motor driver, based on Freescale’s MC33926 full H-bridge, has a wide operating ..
रo 2,802.00 रo 2,919.00
Pololu 1212 MC33926 Motor Driver Carrier
This breakout board for Freescale’s MC33926 full H-bridge has an operating range of 5 – 28 V and can..
रo 1,512.00 रo 1,575.00
Pololu 2130 DRV8833 Dual Motor Driver Carrier
This tiny breakout board for TI’s DRV8833 dual motor driver can deliver 1.2 A per channel continuous..
रo 754.00 रo 786.00
Pololu 2135 DRV8835 Dual Motor Driver Carrier
This tiny breakout board for TI’s DRV8835 dual motor driver can deliver 1.2 A per channel conti..
रo 376.00 रo 391.00
Pololu 2511 DRV8835 Dual Motor Driver Shield for Arduino
This small shield is an easy, economical way to control two small brushed DC motors with an Arduino ..
रo 679.00 रo 707.00
Pololu 2137 A4990 Dual Motor Driver Carrier
This compact breakout board makes it easy to use Allegro’s A4990 dual motor driver, which can contro..
रo 608.00 रo 633.00
Pololu 2990 DRV8838 Single Brushed DC Motor Driver Carrier
This tiny breakout board for TI’s DRV8838 motor driver can deliver a continuous 1.7 A (1.8 A peak) t..
रo 340.00 रo 354.00
Pololu 2961 MAX14870 Single Brushed DC Motor Driver Carrier
This compact breakout board for Maxim’s MAX14870 motor driver offers a wide operating voltage range ..
रo 754.00 रo 786.00
Pololu 2960 BD65496MUV Single Brushed DC Motor Driver Carrier
This compact breakout board for ROHM’s BD65496MUV motor driver offers an operating voltage range of ..
रo 1,071.00 रo 1,275.00
Pololu 2136 DRV8801 Single Brushed DC Motor Driver Carrier
This tiny breakout board for TI’s DRV8801 provides a modern alternative to classic motor drivers suc..
रo 1,044.00 रo 1,087.00
Pololu 1112 Qik 2s12v10 Dual Serial Motor Controller
This powerful motor controller allows variable speed and direction control of two large, brushed DC ..
रo 14,110.00
Pololu 1110 Qik 2s9v1 Dual Serial Motor Controller
This small, inexpensive motor controller allows variable speed and direction control of two small, b..
रo 3,551.00
L298 Dual H-Bridge Motor Driver Module
New L298 Dual H-Bridge Motor Driver Features: Working mode: H bridge ..
रo 235.00
Pololu 2753 DRV8835 Dual Motor Driver Kit for Raspberry Pi
This compact expansion board plugs directly into the GPIO header on a Raspberry Pi B+, Pi A+, Pi 2, ..
रo 754.00 रo 786.00
ULN2003 Stepper Motor Driver Board
ULN2003 Stepper Motor Driver Board A B C D four-phase LED indicates the status of the ..
रo 74.00
Pololu 1392/1394 Jrk 21v3 USB Motor Controller with Feedback
The jrk 21v3 motor controller is a highly configurable brushed DC motor controller that supports fou..
रo 5,638.00 रo 5,873.00
Pololu 767 TReX Jr Dual Motor Controller DMC02
This lower-power, smaller, and lower-cost version of the TReX is the ultimate general-purpose motor ..
रo 11,948.00 रo 14,110.00
Pololu 2968 / 2969 Stepper Motor Driver Carrier, Digital Current Control MP6500
This product is a carrier board or breakout board for the MP6500 stepper motor driver from Monolithi..
रo 520.00 रo 549.00
Pololu 2966 / 2967 Stepper Motor Driver Carrier, Potentiometer Current Control MP6500
This product is a carrier board or breakout board for the MP6500 stepper motor driver from Monolithi..
रo 527.00 रo 549.00
Pololu 2995 G2 High-Power Motor Driver 24v21
This discrete MOSFET H-bridge motor driver enables bidirectional control of one high-power DC brushe..
रo 3,787.00 रo 3,945.00
Pololu 2878 / 2879 STSPIN820 Stepper Motor Driver Carrier
This breakout board for STMicro’s STSPIN820 microstepping bipolar stepper motor driver offers micros..
रo 1,532.00 रo 1,595.00
Pololu 3098 / 3099 Stepper Motor Driver Compact Carrier TB67S279FTG
This breakout board for Toshiba’s TB67S279FTG microstepping bipoloar stepper motor driver is arrange..
रo 816.00 रo 850.00
Pololu 2133 / 2982 DRV8825 Stepper Motor Driver Carrier, High Current
This breakout board for TI’s DRV8825 microstepping bipolar stepper motor driver features adjustable ..
रo 1,286.00 रo 1,339.00
Tags: Pololu, VNH2SP30/VNH3SP30, Dual, Motor, Driver, Carrier, MD03A